
Comprehensive Handbook on Industrial Packaging Machines for Modern Businesses
In today's rapidly evolving market landscape, businesses are increasingly recognizing the critical role of Industrial Packaging Machines in enhancing operational efficiency and product safety. According to a report by Smithers Pira, the global packaging market is projected to reach over $1 trillion by 2024, driven largely by the rise of automated packaging solutions. This rapid growth emphasizes the necessity for modern enterprises to adopt advanced industrial packaging technologies that not only streamline production processes but also reduce material waste and operational costs.
Furthermore, a comprehensive analysis by MarketsandMarkets indicates that the demand for Industrial Packaging Machines will significantly increase, with a projected CAGR of 8.4% from 2020 to 2025. As industries like food and beverage, pharmaceuticals, and electronics expand, the need for state-of-the-art packaging systems becomes paramount. By leveraging these machines, companies can ensure consistent quality, compliance with regulatory standards, and enhanced customer satisfaction, making them crucial investments for businesses aiming to thrive in today’s competitive environment.
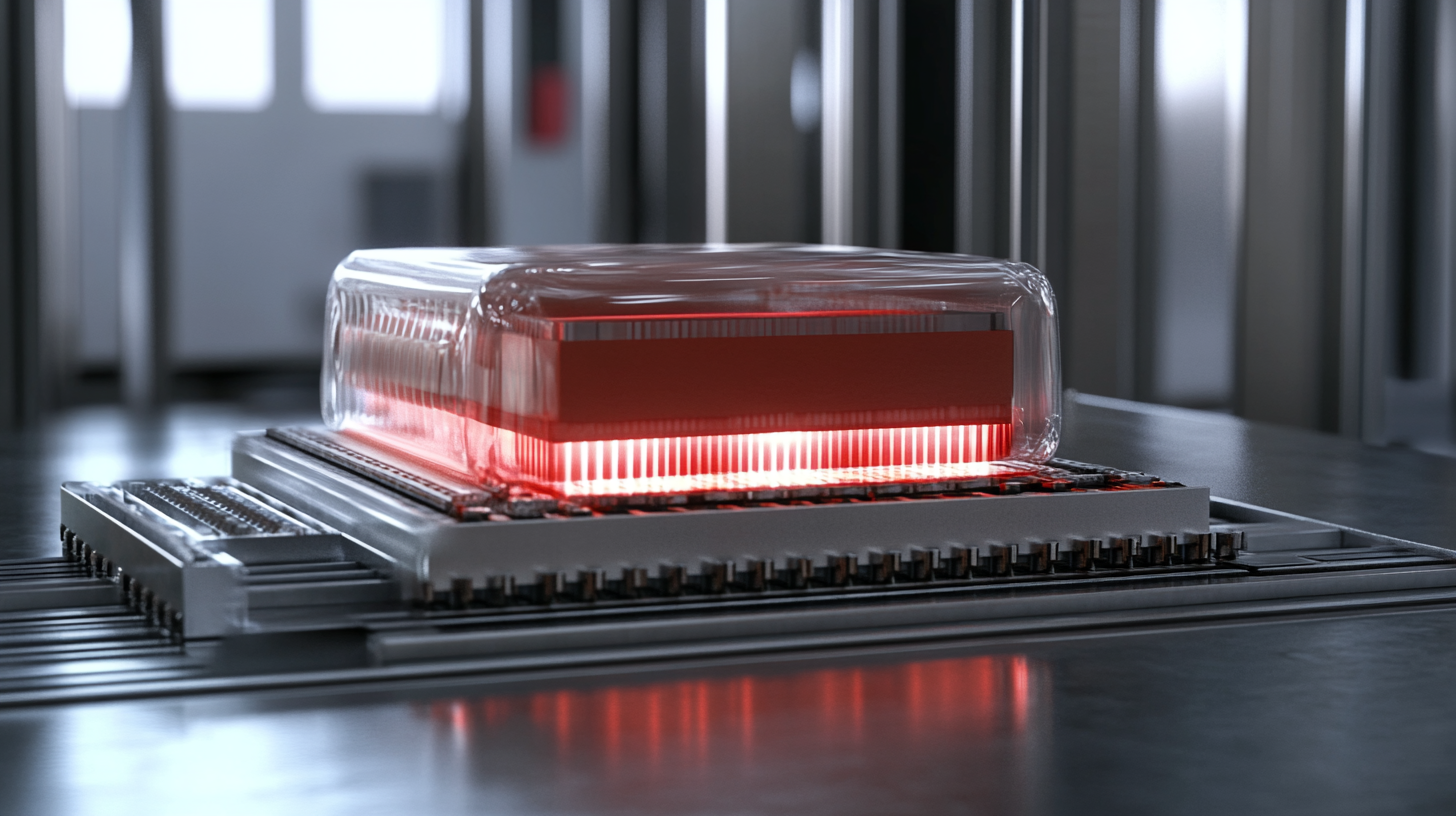
Types of Industrial Packaging Machines: An Overview of Key Technologies
Modern businesses are increasingly relying on advanced industrial packaging machines to optimize their operations and enhance productivity. The array of packaging technologies available today includes aseptic filling machines, automated liquid packaging systems, and vertical form-fill-seal (VFFS) machines, reflecting a significant evolution in engineering and design. Aseptic filling machines, for instance, are gaining traction due to their ability to maintain product sterility while extending shelf life. This technology is projected to grow from a market value of USD 5.8 billion to USD 8.4 billion by 2030, showcasing a compound annual growth rate (CAGR) of 6.1%. This growth is driven by rising consumer demand for shelf-stable beverages and food products. Moreover, the integration of automation, IoT, and robotics into packaging machinery has opened new avenues for efficiency and precision in manufacturing processes. Pneumatics have become a fundamental component of these automated systems, offering reliable motion control that meets the dynamic requirements of advanced packaging applications. As industries navigate this rapidly evolving landscape, adopting cutting-edge technologies will be essential to maintaining their competitive edge and meeting consumer expectations.
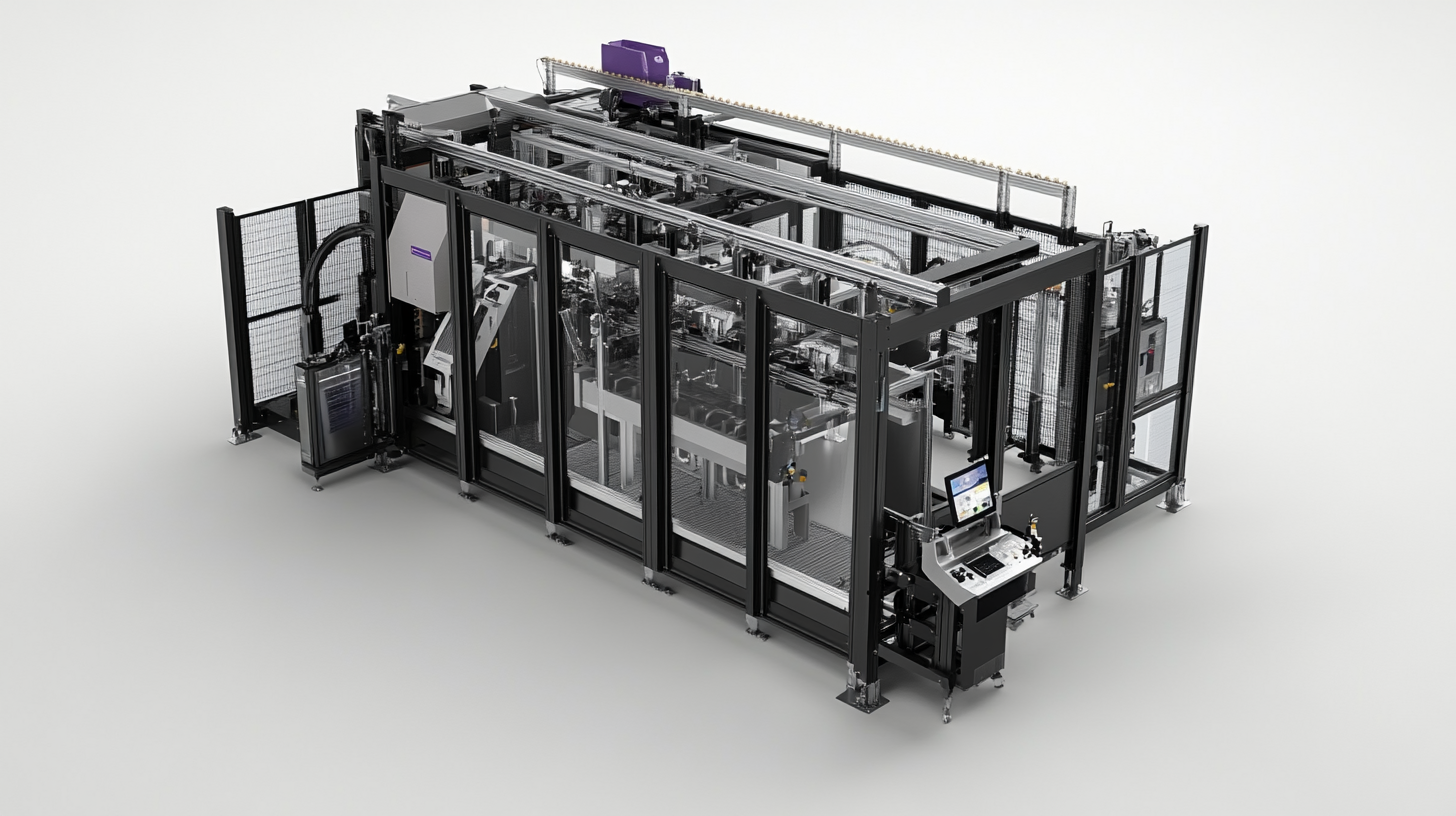
Essential Features to Consider When Choosing Packaging Equipment
Selecting the right packaging equipment is crucial for modern businesses aiming to enhance their efficiency and product appeal. When considering packaging machinery, essential features play a pivotal role. According to a report by Smithers Pira, the global packaging machinery market is expected to reach $50 billion by 2025, driven by innovations in automation and sustainability. Businesses must prioritize machinery that offers versatility and adaptability, given the rapid evolution of product lines and consumer preferences.
Automation capabilities stand out as a key feature when choosing industrial packaging machines. The use of automated equipment can lead to a 30% increase in efficiency, as stated in a 2022 market analysis by Research and Markets. Machinery that integrates seamlessly with existing production lines not only streamlines operations but also reduces labor costs. Furthermore, the ability to adjust packaging sizes and styles easily is critical for businesses facing fluctuating demand.
Another vital aspect to consider is the energy efficiency of the packaging equipment. With rising operational costs, energy-efficient machines can significantly reduce the overall carbon footprint and operating expenses. A report by the Packaging Machinery Manufacturers Institute highlighted that energy-efficient machines can lower energy consumption by up to 25%. This aligns with the growing emphasis on sustainability within the packaging sector, as companies strive to meet both regulatory standards and consumer expectations for eco-friendly practices.
Ultimately, modern businesses must evaluate packaging machinery based on these essential features, as they directly influence productivity, cost-effectiveness, and environmental responsibility. By making informed choices, companies can not only enhance their operational capabilities but also position themselves competitively in a rapidly changing market.
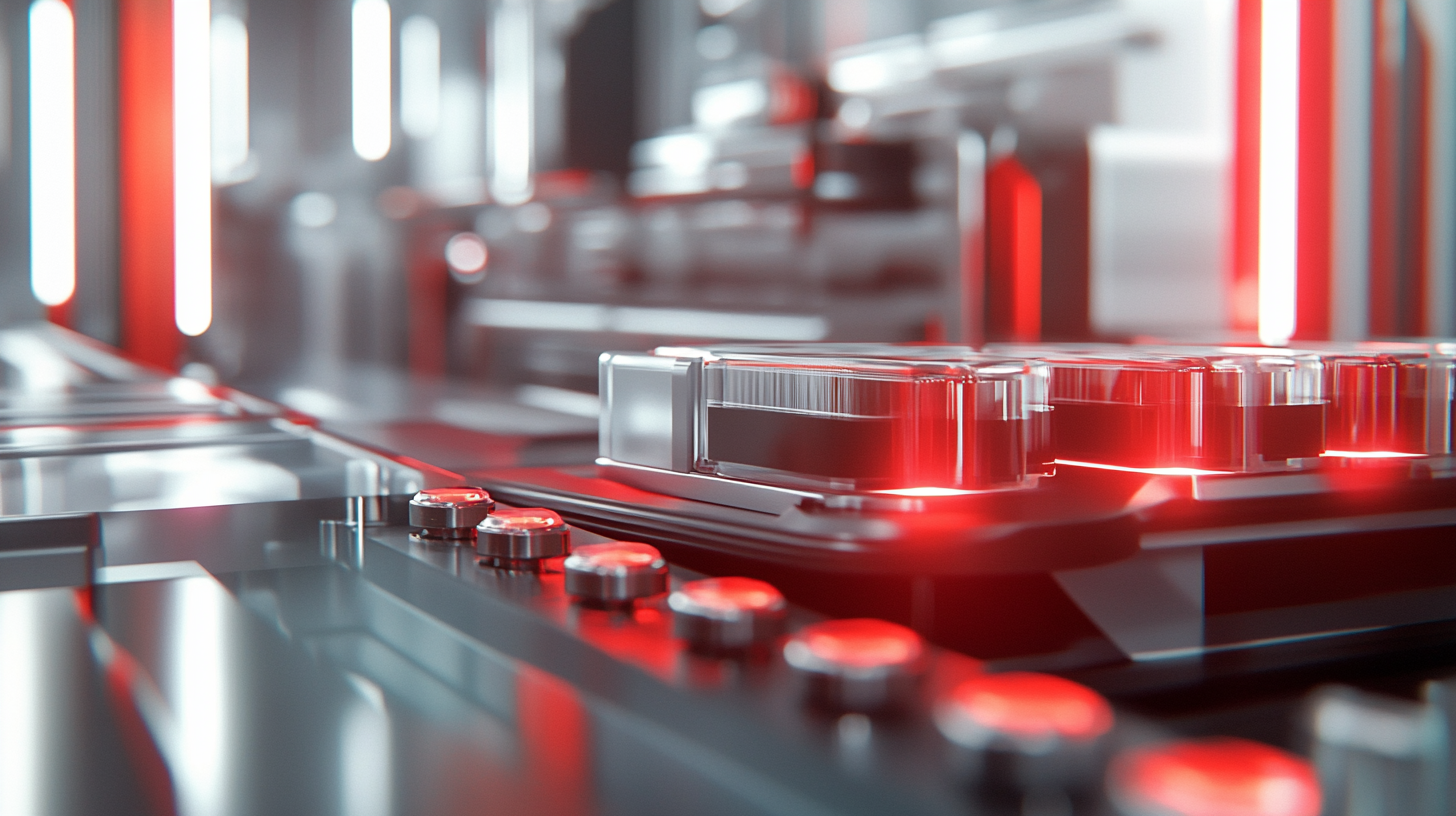
The Role of Automation in Modern Industrial Packaging Solutions
In today’s fast-paced industrial landscape, automation has emerged as a critical component in the realm of packaging solutions. The integration of advanced technologies into packaging machines not only enhances efficiency but also significantly reduces the likelihood of human error. Automated industrial packaging machines can perform various tasks such as filling, sealing, and labeling with remarkable precision and speed, ensuring that products are packaged uniformly and consistently.
Moreover, automation enables businesses to streamline their operations and adapt to fluctuating market demands. Automated systems can quickly reconfigure for different product sizes and packaging styles, allowing companies to pivot seamlessly without the need for extensive manual interventions. This adaptability is especially beneficial in a market landscape that increasingly favors customization and rapid production cycles, where companies must be agile to stay competitive.
The use of automation in industrial packaging also contributes to improved safety and sustainability. By minimizing direct human involvement in hazardous packaging tasks, companies can protect their workforce from potential injuries. Additionally, automated machines are often designed to optimize materials usage, reducing waste and supporting environmentally friendly practices. As modern businesses continue to evolve, embracing automation in their packaging processes is not just an option; it has become a necessity for sustained growth and operational excellence.
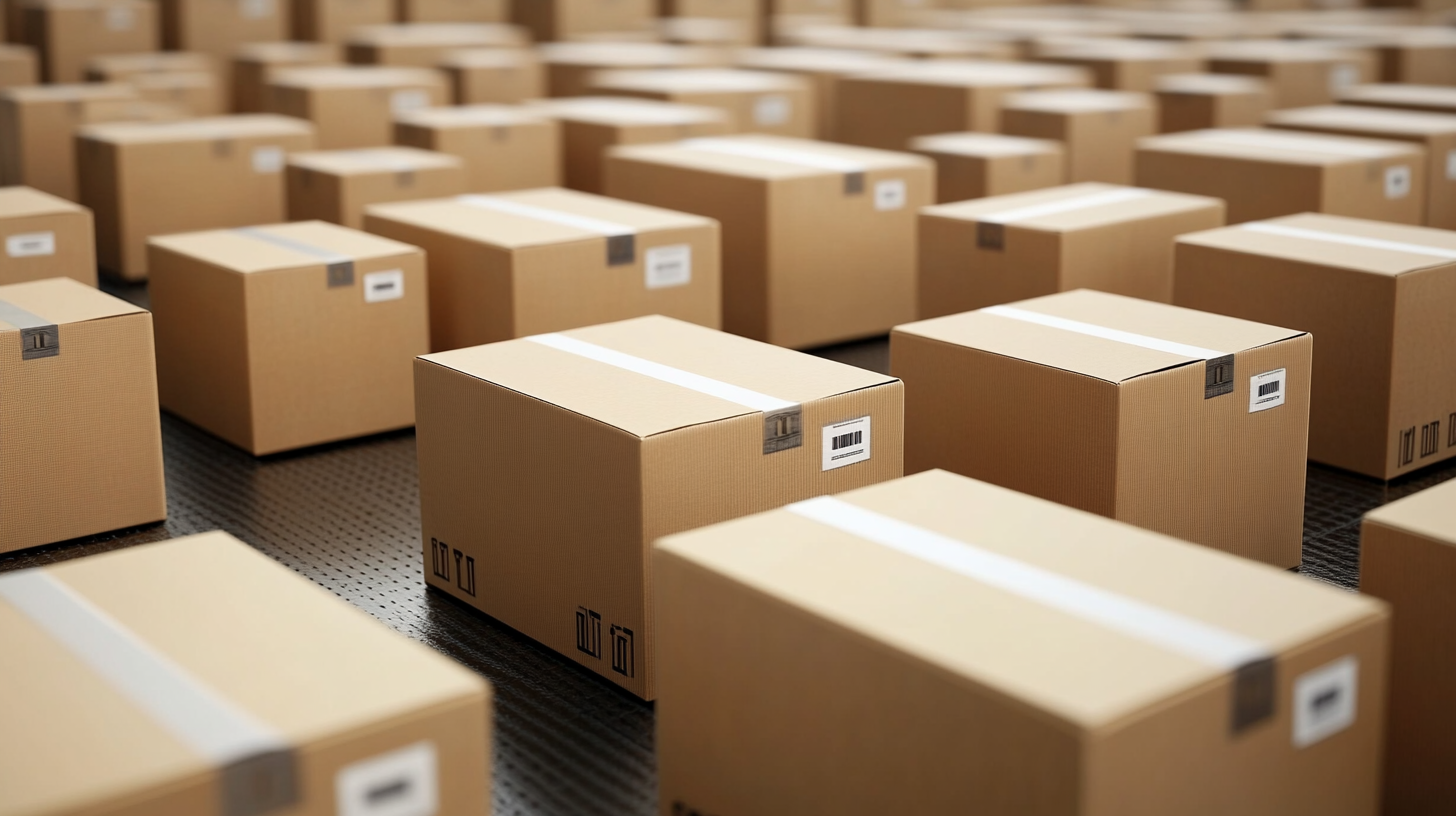
Maintenance Practices for Enhancing the Lifespan of Packaging Machines
Maintaining industrial packaging machines is crucial for ensuring their longevity and optimal performance. Regular maintenance practices not only help in reducing unexpected breakdowns but also enhance the efficiency of operations. A well-maintained machine operates at higher speeds and with greater precision, ultimately leading to cost savings and increased productivity for businesses.
One essential aspect of maintenance is scheduling routine inspections. These inspections should include checking for wear and tear on critical components, lubricating moving parts, and cleaning the machine to prevent dust and debris buildup. Keeping detailed records of these inspections can help identify recurring issues and allow for timely interventions before they escalate into significant problems.
In addition to routine inspections, staff training plays a critical role in the maintenance of packaging machines. Employees who are knowledgeable about the equipment and its functions can spot issues early on and employ best practices while operating the machinery. Regular training sessions can familiarize the team with new technologies and updates, ensuring that everyone is equipped to handle operational challenges effectively.
Lastly, adhering to manufacturer guidelines for maintenance schedules and replacement parts can significantly enhance a machine's lifespan. Investing in quality parts and following recommended maintenance protocols not only prolongs machine life but also supports consistent product quality and operational efficiency. This proactive approach can transform industrial packaging into a smoother and more sustainable process, making it a cornerstone of modern business practices.
Future Trends in Industrial Packaging: Innovations to Watch Out For
The landscape of industrial packaging is evolving rapidly, driven by technological advancements and a growing demand for efficiency and sustainability. As businesses adapt to these changes, several key trends in industrial packaging are set to reshape the future. One of the most prominent innovations to watch is the integration of automation and robotics. Automated packaging machines are becoming increasingly sophisticated, enabling companies to boost productivity and reduce human error. These systems streamline the packaging process, allowing for faster turnaround times and greater consistency, which is crucial in today’s fast-paced market.
Another significant trend is the rise of smart packaging solutions. Incorporating IoT technology, smart packaging not only enhances product security but also provides valuable data on supply chain management. This innovation allows businesses to track products in real-time, ensuring proper handling and storage conditions. Additionally, smart packaging can offer interactive features for consumers, enhancing the overall customer experience and engagement with the product.
Sustainability continues to be a crucial focus, with companies seeking eco-friendly materials and processes. The development of biodegradable and recyclable packaging materials is gaining traction, reflecting a global push towards reducing waste and minimizing environmental impact. As consumers become more environmentally conscious, businesses that prioritize sustainable packaging solutions gain a competitive edge. This trend signifies a shift not just in materials, but in the overall approach to packaging, emphasizing a circular economy that benefits both producers and consumers.